Только в бумагу
Summary:
Фасование в бумагу – день вчерашний? Нет, он и сегодняшний, и завтрашний. Поэтому предлагаем читателям подробно ознакомиться с тем, как происходит упаковка продукта в бумажные пакеты.
Процесс упаковки продукта в бумажные пакеты
Упаковка из бумаги заметно сдала свои позиции под напором пластиков и полимеров. В России производство автоматов для фасования продуктов в бумажные пакеты практически прекратилось в первой половине 90-х годов. Все эти годы для фасования в бумагу несколько предприятий предлагали потребителям лишь ручное и полуавтоматическое оборудование, пусть и облегчающее труд фасовщиков, но все же требующее от них физических усилий. Лишь в самое последнее время предприняты первые, увы, весьма робкие, шаги по воссозданию сектора отечественного упаковочного машиностроения, ответственного» за бумажную упаковку. Наступление полимеров в упаковочных процессах вполне понятно. Это более красивая упаковка, которой, подбором слоев упаковочного материала, легче предать какие-то свойства, необходимые для лучшего хранения продуктов. Да и оборудование, оперирующее с полимерными упаковочными материалами, чаще всего проще с конструктивной точки зрения, менее материало- и энергоемко, занимает меньшую площадь, проще в изготовлении и наладке.
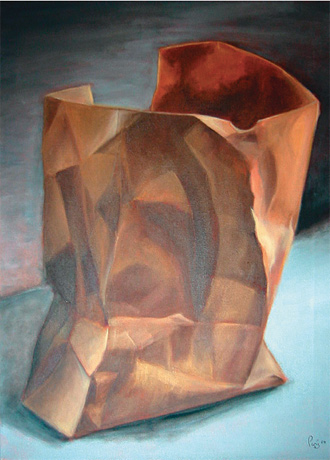
Но при всех достоинствах полимерной упаковки есть преимущество и у бумажной. Сложно сказать, производство чего, полимеров или бумаги, наносит больший вред природе. Но бумажный пакет, выброшенный безалаберной рукой и не украшающий пейзаж, сразу же начинает гнить и разлагаться на природные составляющие. А вот о сроках естественного распада полимеров, похоже, не знает никто. Называются сроки от 80 лет до столетий. Во всяком случае, первые образцы полиэтиленовой пленки, созданной в 1946 году, если не пошли в утилизацию, где-то еще валяются.
С все больше применяющимися сейчас разлагающимися полимерами тоже не все так просто. Некоторые специалисты говорят о большом вреде, причиняемом почве при попадании в нее составляющих разлагаемых полимеров. Бумажная упаковка вряд ли когда-нибудь исчезнет совсем. Бумага вместе с картоном еще долго будет использоваться при создании элитной и подарочной упаковки. Но главное, что поддерживает бумажную упаковку, – это то, что некоторые продукты все же лучше хранить в бумаге. Прежде всего, это крупы и, еще более, хлебопекарная мука и смеси на ее основе. Поэтому фасовочно-упаковочное оборудование, использующее бумагу, будет существовать и развиваться, по крайней мере, очень долго.
Немного истории
Бумага далеко не старейший упаковочный материал. Есть материалы и древнее: глина (точнее, керамические изделия из нее), дерево, камень. Даже изделия из стекла применялись для наполнения жидкостями за сто лет до Рождества Христова. Первые сведения о применении бумаги в упаковывании относятся к VI веку. Тогда в Германии у печатников существовала практика переплетать только те книги, на которые находился покупатель. Ну, а листы невостребованных ниг продавались торговцам для завертывания в них товаров. В середине 1600-х годов в Англии в бумагу упаковывали только самые ценные товары, на тот момент это были табак и чай. Широкого использования бумаги для получения упаковок не могло быть по причине ее дороговизны, главным образом, из-за ручного изготовления. 1798 год можно считать годом, который вызвал отношение к бумаге как к упаковочному материалу, причем, в самом современном понятии. В этом году во Франции был изобретен первый бумажный станок, а в Германии литография. И бумага сразу стала дешевле, и появилась возможность сравнительно недорого наносить на нее изображения, в том числе цветные. Бумага и печатные изделия из нее стали доступнее, когда в 1807 году в Англии началось производство бумаги в рулонах, а в 1879 году был изобретен более дешевый способ печати – офсет. В промежутке между этими событиями, произошли еще несколько, совместными «усилиями» которых бумага стала по-настоящему упаковочным материалом. В 1852 году в США появился первый станок для изготовления бумажных пакетов, в 1860 – более рациональный и удобный, а с 1870 года стали промышленно изготавливать бумажные пакеты с плоским дном.
Американский историк упаковки Томас Хайн считает рубеж XIX и XX веков тем временем, когда сложилось понятие современной упаковки. Именно в последнее десятилетие позапрошлого и первые годы прошлого века тару и упаковку для самых разнообразных продуктов стали получать промышленным способом с производительностью, достаточно сопоставимой с сегодняшней. К тому же времени относятся и первые попытки создания оборудования для фасования продукции.
В отношении бумажной упаковки можно привести пример, что в самом начале ХХ века появилась известная поныне американская компания по производству фасовочно-упаковочного оборудования Hayssen, первым образцом техники которой был автомат для изготовления бумажных пакетов.
Взгляд на машины
В отличие от оборудования для фасования различных продуктов в гибкие термосвариваемые материалы, технологические схемы которого можно было рассматривать практически не касаясь свойств фасуемых продуктов, способов их дозирования и, соответственно, дозаторов, сводя, по сути, все к рассмотрению упаковочных частей автоматов, то при рассмотрении оборудования для фасования в бумажные пакеты так не получится.
Здесь, в зависимости от свойств фасуемых продуктов и установленных дозаторов в технологических схемах почти обязательно проявляются какие-то изменения. О какой-то полной «базовости» упаковочной части автоматов здесь не может быть и речи. Что, конечно, не исключает возможности применения какого-то узла с одного автомата на другом, предназначенном для иного продукта. Поэтому и фасуемых продуктов и дозаторов придется обязательно коснуться. Правда, предупредим, что «касание» будет поверхностным. О свойствах продуктов подробнее пусть говорят другие специалисты, а о конструкциях дозаторов, надеемся,разговор будет в других статьях. Хотя процессы фасования продуктов в бумажные пакеты при некоторых условиях можно производить на оборудовании непрерывного действия, все же подавляющее число единиц техники является оборудованием периодического действия. Самое главное различие автоматов для фасования в бумажные пакеты и технологических схем их работы заключается в том, используют ли они готовые пакеты или сами их образуют из полосы бумаги, поступающей с рулона. Второе различие оборудования заключается в том, сколько раз на оборудовании производится дозирование. Это зависит от свойств фасуемого продукта, величины дозы и применяемого дозатора. Третье различие – в способе заделки верха пакета.
Наиболее распространены: заделка пережимом верха с образованием замка-«гребешка» и приклеивание этого «гребешка» к пакету. «Гребешок» может быть получен одним или двумя перегибами свободного от продукта верха пакета. Есть еще способ, заключающийся в завороте двух параллельных кромок внутрь пакета и приклейке образовавшихся уголков. Следует отметить, что механическое манипулирование пакетами с «гребешком», в частности, автоматическое создание групповой упаковки из бумажных пакетов с продуктом, затруднено. Поэтому заделка пакетов замком-«гребешком» на высокопроизво-дительном оборудовании практически не применяется.
Для описания различных технологических схем фасования продуктов использовались схемы работы конкретных автоматов, марки которых, за исключением одного случая, не приводим. Выбор автоматов для описания их работы делался исходя из того, чтобы, по возможности, охватить различные варианты технологических схем и операций, производимых оборудованием. Возможны другие технологические схемы работы оборудования, но все они сочетают операции, описанные ниже.
ФАСОВОЧНЫЕ АВТОМАТЫ,ИСПОЛЬЗУЮЩИЕ ГОТОВЫЕ ПАКЕТЫ
Автоматы без контрольного взвешивания и досыпки
Это наиболее простое оборудование, наименее габаритное. Заклейка пакета может производиться замком в форме «гребешка» или с загибом этого "гребешка". Имеются два заметных конструктивных отличия оборудования. Когда засыпка дозы осуществляется при закреплении пакета на воронке, через которую в пакет поступает продукт, и когда пакет закрепляется на каком-то несущем органе, чаще дискретно вращающемся роторе. Первое чаще применяется при фасовании муки (пылящих продуктов), второе – при фасовании других продуктов (круп, сахара).
Заделка верха замком-«гребешком»
Одним из самых хорошо отработанных на протяжении долгих лет способом, по которому работает оборудование для фасования муки, является способ, когда верх раскрытого пакета при засыпке дозы надевается на воронку и прижимается к ней (Рисунок 1).
Рисунок 1
Готовые пакеты, предварительно заложенные в кассете (1), захватываются (2), переносятся, раскрываются и надеваются на воронку (3). Боковая часть воронки растягивает пакет, а механизм прижима плотно прижимает его к воронке. Тут пакет наполняется продуктом. После этого пакет передается на приемный стол (4), который переносит его чуть в сторону (5). Механизм подачи перемещает его на механизм подъема (5), который перемещает его к конвейеру (6). Последний периодически передает пакет на механизм утряски (7). После утряски пакет обжимается (8), у горловины пакета боковые фальцы заправляются внутрь (9), после чего верхняя часть пакета сжимается (10). Далее производится биговка и отрезка верхней кромки пакета (11). На верхнюю часть пакета наносится клей (12), производятся первый (13) и второй (14) перегибы. Затем к свернутой кромке пакета прижимаются две нагретые губки, которые осуществляют склеивание (15). Заполненный и заклеенный пакет (16) выходит с автомата.
Так же хорошо в свое время «поработал» и не потерял своей актуальности способ, где часть операций на пакете (включая дозирование) осуществляется при остановках ротора, в карманы которого помещаются раскрытые пакеты (Рисунок 2).
Рисунок 2
Уложенные заранее пакеты в плоскосложенном состоянии находятся в кассете (1). Когда ротор находится в состоянии выстоя, пакет забирается из кассеты и вводится в гнездо ротора (2), где верх пакета раскрывается и зажимается прижимами. При остановке ротора в раскрытую часть пакета подают сжатый воздух и одновременно расправляют дно пакета, что обеспечивает полное раскрытие пакета (3). При дальнейшем перемещении пакета на позицию дозирования может производиться контроль наличия пакета в гнезде. После перемещения пакета и остановки его на следующей позиции производится помещение в пакет дозы продукта (4). Наполненный пакет при дальнейшем перемещении ротора опускается на конвейер (5), который вначале переносит пакет в механизм складывания верха. В зависимости от типа применяемого пакета, следующая операция может быть различной. Или производится растяжка пакета (6а) для пакета с шестиугольным дном, или образование складок (боковых фальцев) (6б) для пакета с прямоугольным дном и сплющивание (7). При дальнейшем движении пакета производится зажим верха пакета (8) цепями или бесконечными лентами конвейеров, биговка и отрезание верхней кромки (9), нанесение клея (10), первый перегиб (часто с электроподогревом) верха пакета (11), второй перегиб верха пакета (12) (тоже с подогревом) и обжим «гребешка» (13 и 14). Наполненный и заклеенный пакет транспортером готовой продукции отводится на дальнейшие операции.
Заделка верха в замок с приклеиванием « гребешка»
Такая заделка, а заодно и придание пакету формы правильного параллелепипеда, сейчас используется заметно чаще. В принципе, схема, которая описана ниже, не сильно отличается от предыдущей. Но некоторые действия с пакетом производятся при нахождении его на операционном роторе, а не на конвейере, как описано выше. В качестве еще одного отличия можно добавить, что на некоторых автоматах сдавливание пакета произдится не на конвейере, а на роторе.
Схема представлена на Рисунке 3.
Рисунок 3
Пакеты из кассеты (1) переносятся (2) и устанавливаются в гнездо ротора (3). Затем раскрывается верх (4) и дно (5) пакета, расправляется верх пакета (6), и он подается на наполнение продуктом (7). На позиции (8) осуществляется утряска продукта в пакете. Далее начинается формирование верха по узким (9) и широким (10) стенкам. Пакет из гнезда (11) поступает на конвейер, которым вводится сначала в нижние (12), а потом и в верхние (13) направляющие. Зажимается верх пакета (14) с дальнейшей его прокаткой (15). После этого отрезается верх пакета (16) и наносятся биговки (17). На позициях 18, 19 осуществляется перегиб и прокатка замка пакета, а на позиции 20 – нанесение клея на замок. На последующих операциях производится электроподогрев клея (21), прижим замка-«гребешка» к верху пакета (22) и приклеивание верха пакета (23). Готовый заполненный пакет выходит из автомата (24).
Автоматы с контрольным взвешиванием, а также с досыпкой продукта и с заполнением пакета продуктом по частям, более современны. Но описание этих процессов мы не приводим здесь, расскажем о них ниже, где будет рассматриваться более «серьезное» оборудование.
Фасовочные автоматы,изготавливающие пакеты
Заметно позже оборудования, где используется готовый пакет, появились автоматы, где пакет образуется из ленты бумаги непосредственно на оборудовании. Сказать, что оборудование, образующее пакет и фасующее в него сыпучие продукты, получило большее распространение, нежели оборудование, использующее готовые пакеты, нельзя, оно при большой производительности имеет и большие габариты, поэтому предназначено для крупных фасующих предприятий.
Автоматы с двумя операционными роторами
Заделка верха пакета приклеиванием углов
Пример работы автомата, образующего одинарный пакет, заполняющего его хорошо сыпучим продуктом и запечатывающего его образованием и приклеиванием уголков, приведен на схеме на Рисунке 4.
Рисунок 4
Бумага для изготовления пакетов сматывается с рулона (1) и проходит через механизм нанесения рисунка и реквизитов (2). Далее бумага подается через механизмы нанесения клея (3) и отрезки заготовки (4). Отрезки бумаги поступают на оправки, расположенные в описываемом автомате на первом операционном (пакетоделательном, или тарообразующем) роторе, где происходит обжим бумаги (5) и склеивание продольного шва (6). На следующих позициях сформированный пакет проходит операции заделки узких клапанов дна пакета (7), заделки заднего и переднего клапанов дна пакета (8) и прижима дна пакета (9), после чего пакет специальным механизмом снимается с оправки (10).
Механизм передачи пакета осуществляет поворот пакета (11) и установку его в карман второго операционного (упаковочного) ротора (12). При движении пакета в кармане ротора последовательно происходят следующие операции: заполнение пакета продуктом (13) с предварительным контролем уровня продукта, утряска продукта (14 и 15), контроль уровня продукта (16), выталкивание бракованного пакета (17), трамбовка продукта (18), загиб первого узкого клапана и разведение широких клапанов пакета (19), загиб второго узкого клапана пакета и разведение широких клапанов пакета (20), внутренняя проклейка пакета (21), прижим заделанных клапанов (22), внешняя проклейка пакета (23), заделка заднего уголка (24), заделка переднего уголка (25), прижим верха пакета (26), выталкивание его из кармана ротора (27), подача пакета с продуктом на конвейер (28). Для обеспечения качественного заклеивания верха пакета при их движении на конвейере (29) верх пакетов постоянно прижимается верхним конвейером. Далее сформированные, заполненные и заклеенные пакеты попадают на выдающий конвейер автомата, с которого поступают на дальнейшие операции (30).
Автоматы с пакетоделательным ротором и операционным (упаковочным) конвейером
Заделка верха в замок с приклеиванием « гребешка» Двойное дозирование
Теперь рассмотрим автомат для фасования плохо сыпучих продуктов с двойным дозированием. Технологическая схема работы такого оборудования представлена на Рисунке 5.
Рисунок 5
Тянущие ролики подают бумагу с рулона (1) к оправкам тарообразующего агрегата (пакетоделательного ротора). По пути движения на нее в соответствующих местах специальным механизмом наносится печать (2), производится просечка (3) и валиками клеевого механизма смазка клеем пределенных участков бумаги (4). Производится отрезка заготовок (5), затем формируется пакет, т.е. заготовка, при движении вверх площадки, на которой она находится, обтягивает оправку ротора. В конструкциях некоторых автоматов предусмотрена возможность подогрева бумаги перед поступлением ее на ротор, с целью обеспечения более надежной склейки пакетов. При помощи лап (6), загибающих свободные концы заготовки, образуется продольный шов, быстрой заделке которого способствует прижим, опускающийся на шов (7). При повороте ротора заделывается дно пакета (8, 9). В позиции 10 происходит подогрев и прижим дна пакета. При помощи специального механизма, которому в некоторых конструкциях «помогает» сжатый воздух, вводимый внутрь оправки, на позиции 11 пакет снимается с оправки, поворачивается (12) и подается в гнездо транспортной цепи упаковочного агрегата (13). В некоторых конструкциях для передвижения пакета и установки в гнездо используется промежуточный ротор (ротор передачи тары). Далее при периодическом движении транспортной цепи с пакетом производится отмер и засыпка в него половины дозы продукта (14), утряска продукта (15), засыпка второй половины дозы (16) с помощью второго дозатора. Далее снова производится утряска продукта в пакете (17). После утряски срабатывает механизм раскрытия гнезда, и пакет поступает на грузоприемную площадку весов (18), где контролируется масса продукта в пакете. Если доза продукта имеет отклонения, выходящие за пределы допустимых, то этот пакет выталкивается из гнезда (19). Производится еще одна, но уже более длительная, утряска (20, 21), потом механизм обжима придает пакету четкую форму (22). На следующей позиции (23) производится четвертая по счету утряска. В результате подъема столика с пакетом (24) уровень продукта в пакете выставляется на заданную высоту, что создает удобство при заделывании пакета. Затем формируется верх пакта (25), т. е. образование боковых складов и плоское складывание верха пакета, а в позиции (26) обрезка излишков бумаги и нанесение зигов (27). Излишки бумаги удаляются, например, с помощью сжатого воздуха. Далее, верх пакета загибается (28) и проводится между неподвижными планками 29, окончательно принимая форму «гребешка». В позиции 30 на «гребешок» наносится клей, «гребешок» подгибается (31) и прижимается к пакету (32). Пакет выталкивается из гнезда цепного конвейера упаковочного агрегата (33). Дополнительно, для обеспечения качественного склеивания, пакеты на выходе из автомата проходят между двумя конвейерами (34). С автомата отводится готовый пакет (35).
На некоторых автоматах можно получать не только одинарный бумажный, но и двойной пакет. В этом случае, возле пакетоделательного ротора устанавливаются два рулона бумаги, два устройства нанесения клея и т. д. Вначале на оправке изготавливается пакет, а потом он покрывается еще одним слоем бумаги со второго рулона. При необходимости получения одинарного пакета, второй агрегат не задействуется, а позиции положения оправок, задействованные при получении двойного пакета, в этом случае являются «холостыми».
Двойное дозирование с досыпкой
Фасование с двойным дозированием и с досыпкой продукта рассмотрим на примере советского автомата А5-АФЛ для фасования муки дозой 2 кг, разработанного в 80-е годы, на основе технических решений, полученных по лицензии фирмы Robert Bosch, и выпускавшегося до середины 90-х годов. Технологическая схема этого автомата (Рисунок 6) имеет некоторые отличия от описанной выше.
Рисунок 6
Бумага подается при помощи тянущих валиков с рулона 1 к оправкам. По пути ее движения выполняются операции: нанесение красочной печати одного цвета (2), сушка нанесенной печати ультрафиолетом (3), нанесение печати другого цвета (4), сушка нанесенной печати (5), просечка клапанов дна (6), нанесение продольных бигов (7), нанесения клея для продольного шва и донышка (8), отрезка заготовки пакета (9). Формовка пакета, заключающаяся в обтягивании оправки заготовкой (10), загибе свободных концов заготовки (11) и образовании продольного шва (12) происходит так же, как описано ранее. Как и там, быстрой заделке продольного шва способствует прижим продольного шва с подогревом (13). Далее следуют операции по заделке дна пакета – подгиб створок: верхней узкой (14), нижней узкой (15), правой широкой (16) и левой широкой (17). После чего следует прижим дна и продольного шва с подогревом (18…20) и нанесение маркировки (21). Пакет снимается с оправки (22), поворачивается (23) и передается в гнездо операционного (упаковочного) конвейера(24). Наличие установленного пакета в гнезде контролируется (25). При перемещении пакета операционным конвейером производятся следующие операции: заполнение пакета половиной дозы продукта (26), утряска (27), заполнение продукта менее чем половиной дозы продукта (28), утряска (29), взвешивание продукта в пакете (30) (по результату взвешивания определяется величина необходимой досыпки продукта), досыпка продукта (31) до требуемого номинала и снова утряска (32). Следует еще одно взвешивание пакета с продуктом (33), выталкивание бракованного по массе продукта в нем пакета (34) и еще утряска (35), обжим пакета (36), снова утряска (37).
При дальнейшем перемещении пакета осуществляются операции: по контролю уровня продукта и выравниванию пакета по уровню (38), складыванию верха пакета (почти так же, как описано ранее) (39), нанесению биговок (40), отрезке верхней кромки пакета (41), первому перегибу гребешка (42), обжиму первого перегиба (43), второму перегибу гребешка (44), нанесению клея на «гребешок» (45), прижиму «гребешка» к пакету (46), выталкиванию пакета из гнезда (47), передаче пакета на конвейер (48), перемещению пакета (49), выдаче готовых пакетов (50).
Операции по фасованию и упаковыванию
Здесь мы подробнее поговорим об операциях, осуществляемых на автоматах, и о том, как они выполняются. Дозирование продукта осуществляется с помощью весовых и, чаще, объемных дозаторов различных типов. Весовые дозаторы специальной конструкции очень редко примененяются для отмера и выдачи дозы муки. В автомате, конструкция которого была взята для описания технологической схемы на Рисунке 1, использовался именно весовой дозатор.
Но наиболее часто для дозирования хлебопекарной муки, смесей на основе муки, других трудно сыпучих продуктов применяется объемный шнековый дозатор. Двойное дозирование и двойное дозирование с досыпкой продукта применяется при дозировании продукта шнеком. Двойное дозирование применяется при получении крупной дозы пылящего продукта. Это, к примеру, может быть мука дозой 2 кг. Дело в том, что получение крупной дозы за один прием отрицательно скажется на производительности. Кроме того, поднимаемая при засыпке крупной дозы пыль может отрицательно сказаться на последующей заклейке пакета. Двойной засыпкой дозы продукта с утряской между засыпкой половин доз запыление стенок пакета стремятся уменьшить. Для повышения точности дозы фасуемого продукта (а шнековый дозатор наименее точный из всех дозаторов) применяется досыпка продукта после предварительного определения массы продукта в пакете. Для хорошо сыпучих продуктов (крупы, сахар и т. п.) в основном применяется объемный стаканчиковый дозатор. Стаканчиковый и весовой дозаторы позволяют получить на этих продуктах достаточно точную дозу, так что досыпка здесь не требуется. В подавляющем большинстве случаев можно обойтись и без контроля массы продукта в пакете.
Захват и выведение сложенного пакета из кассеты, а также перенос его в рабочий орган, производящий операции с пакетом, осуществляется, чаще всего, вакуумными захватами (присосками). Также вакуум-присосками чаще всего осуществляется раскрытие пакета. Но тут нередко появляются дополнительные органы, которые помогают раскрывать пакет. Это могут быть специальные стержни (позиция 6 Рисунка 3), которые вводятся в приоткрытый присосками пакет растягивают его. В технологической схеме на Рисунке 1 воронка, через которую засыпается продукт, кроме прочего, выполняет роль растягивающего пакет элемента. Может использоваться и сжатый воздух, который подается в приоткрытый пакет. В некоторых конструкциях (добавим, и при использовании некоторых вариантов пакетов) дополнительно отводится донышко сложенного пакета. Это проделывает устройство с рабочим элементом в виде крючка.
Контроль наличия пакета в транспортирующем элементе, осуществляемый перед дозированием, — операция, позволяющая избежать потерь (или, по крайней мере, сократить их) продукта. Он чаще всего осуществляется фотоэлементом. Складывание верха наполненного пакета осуществляется в таком порядке: в открытый верх пакета вводятся планки, которые первоначально растягивают широкие стенки пакета, потом начинают сдвигаться (складываться) с одновременным движением навстречу друг другу лапок, складывающих узкие стенки пакета и заправляющих их между планками для широких стенок, потом происходит обжим сложенного верха другими лапками.
Нанесение биговок или просто операция «биговка» проводится с целью получения четких продавленных линий на пакете, по которым будет складываться его верхняя часть перед заклеиванием или на бумаге перед оборачиванием оправки, на которой образуется пакет. Биговка при работе устройства в периодическом режиме (например, биговка верха пакета) осуществляется прижатием к бумаге планок, в одной из которых имеется один (при одинарном перегибе «гребешка») или два (при двойном перегибе) выступа, а в другой соответственно одна или две впадины. При работе устройства в непрерывном режиме (получение биговок, по которым будет складываться пакет, при движении бумаги с рулона) биговка осуществляется при проводе бумаги между двумя роликами, на одном из которых имеются впадины, а на другом выступы. В некоторых автоматах биговка верха сложенного пакета совмещена с операцией отрезания верхней кромки пакета.Отрезание верхней кромки пакета проводится чаще всего во взаимодействии с операцией выравнивания верхнего уровня продукта в пакетах (см. ниже), в момент выстоя пакета с продуктом взаимодействием подвижного и неподвижного плоских ножей. Таким же образом чаще всего осуществляется отрезание от бумаги, движущейся с рулона, заготовки пакета. Но встречается оборудование, где эта операция осуществляется контактом вращающегося на валу плоского ножа и твердосплавной пластины.
Нанесение просечек будущих клапанов (створок) дна пакета при получении заготовки осуществляется при движении бумаги секторными ножами, установленными на валах. Бумага проходит между таким валом и другим, в котором имеются прорези. При попадании секторного ножа в прорезь осуществляется просечка.
Перегиб верха пакета (одинарный) с целью получения «гребешка» производится в два этапа: вначале взаимодействием двух лапок, одна из которых пирается в биговку, а вторая сгибает свободный конец пакета под углом в 900, а затем, когда первая лапка отведена, производится складывание вдвое. Двойной перегиб повторяет эти этапы дважды.
Нанесение клея при заделке верха пакета осуществляется при контакте пористого материала, на который избыточным давлением подается клей, с бумагой или (редко) форсункой. Нанесение клея на заготовку пакета чаще всего производится клеевыми секторами, которые поочередно контактируют с бумагой и валом, получающим клей из клеевой ванной. Операция выравнивания пакетов по верхнему уровню продукта в них, осуществляемая на некоторых автоматах перед складыванием пакета, биговкой и отрезанием верхней кромки, направлена на то, чтобы получить точный размер незаполненного верха пакета, предназначенного для перегиба и склейки. Дело в том, что величина (по объему) дозы фасованной продукции может быть разной в разных пакетах, может разниться и длина пакета. Для хорошего перегиба верха и склейки требуется, чтобы расстояние между верхним уровнем продукта в пакете и его верхней кромкой было одинаково. Суть операции выравнивания уровня продукта в пакете пояснена на Рисунке 7.
Рисунок 7
Нанесение переменных реквизитов (дата фасования, срок годности, номер смены и т. п.) и печати на бумагу перед формированием пакета. Если нанесение переменных реквизитов – операция необходимая и даже обязательная, т.к. эти реквизиты являются обязательной информацией для потребителя фасованной продукции, то отношение к нанесению рисунка на бумагу не столь однозначно. Современное фасовочное оборудование,формирующее бумажный пакет, действительно может наносить рисунок в одну,две и даже три краски (большее число красок встречать не приходилось), в том числе, по способу флексопечати (Рисунок 6). В некоторых случаях это оправданно. Но возможности полиграфистов сейчас возросли, и смогут ли не специалисты в полиграфии –фасовщики – получать такой рисунок на пакете, чтобы их упаковка могла соперничать с упаковкой, где рисунок нанесен в типографии? Думается, что вряд ли. Да и, как бы хорошо не был изготовлен и отлажен узел печати, фасовочно-упаковочный автомат все же не полиграфическое оборудование и стоит опасаться за качество изображения. Обязательная же операция нанесения переменных реквизитов (маркировки) без разницы когда, где и в каком месте готового или образуемого пакета они наносятся, чаще всего производится одним из следующих способов: краской или тиснением (выдавливанием оттиска цифр на бумаге).
Последнее особенно эффективно, когда совмещено с прогреванием материала, как на рисунке 6, тиснением через красящую ленту; самым современным способом – с помощью принтера. Обжатие пакета с продуктом специальным механизмом при выполнении ряда других фасовочных операций способствует получению хорошо наполненного продуктом пакета правильной формы. Этому же способствует и утряска пакета с продуктом. Амплитуда придаваемых колебаний, длительность утряски, число этих операций при прохождении технологического цикла операций по фасованию и упаковыванию продуктов зависит от свойств фасуемого продукта. Для круп, сахара-песка и подобных продуктов обычно достаточно не длительной по времени утряски (профессионалы в этом случае обычно употребляют термин: встряхивание), а вот для продуктов, в обычном состоянии сильно насыщенных воздухом (мука), утряска – достаточно длительная операция, да еще и неоднократно повторяемая.
Что дальше?
Каковы же дальнейшие операции с бумажными пакетами, наполненными продуктом? Для удобной доставки в магазины и для удобного хранения их на складах, потребительские бумажные упаковки с продуктом объединяют, создавая групповые упаковки, а иногда и специальные транспортные. При использовании малопроизводительного оборудования групповую упаковку создают чаще всего вручную. Для современного оборудования, на котором получают потребительскую упаковку, характерным является то, что оно может комплектоваться оборудованием (полуавтоматами, а чаще автоматами), на котором потребительские упаковки объединяются, и из них создаются групповые упаковки. Фасовочный автомат, снабженный адаптированным под него устройством создания групповой упаковки, тогда превращается в комплексную упаковочную линию, где решены вопросы потребительского, группового, а возможно, и транспортного упаковывания.
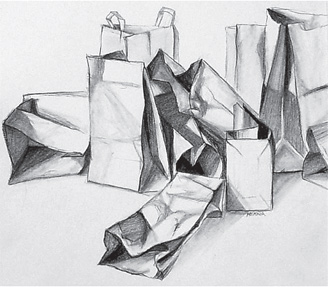
Наиболее распространенные способы создания групповой упаковки из бумажных пакетов с продуктами таковы: создание блока из упаковок и обертывание его бумагой, создание блока из упаковок и обертывание его термоусадочной пленкой с последующей тепловой усадкой, создание блока с обертыванием растягивающейся пленкой (стретч-пленкой), укладка потребительской упаковки в короба из гофрированного картона. С распространением торговли в магазинах самообслуживания появился еще один способ: укладывание потребительской упаковки в специальные контейнеры, впоследствии помещаемые непосредственно в торговом зале универсама.
Операции создания групповой упаковки для бумажных пакетов с продуктом, по сути, не намного отличаются от подобных операций, проводимых с другими видами упаковок, поэтому они будут рассмотрены в другой работе, посвященной групповому упаковыванию продукции.
Владимир УЛЬЯНОВ
2006 #2
|